Beautifully engraved certificate from the United States Cotton Ginning Company issued in 1913. This historic documenthas an ornate border around it with the company's name on top. This item has the signatures of the Company's President, Norman Paine Pearse and Secretary and is over 93 years old. COTTON GINNING TRENDS By Thomas D. Valco, USDA ARS, Stoneville, MS Bill M. Norman, National Cotton Ginners Association, Memphis, TN Abstract The United States cotton ginning industry has seen many new trends over the past years. These trends include the consolidation of gin plants, adoption of mechanically harvested cotton, universal density bales and net weight trading, long-term cottonseed storage at the gin, adoption of HVI cotton classing and gin process control, electronic data handling, and increasing environmental regulations. Gin numbers have steadily declined while annual volume and operational costs continue to increase. Gin owners are looking for every opportunity to improve the bottom line by increasing capacity, volume, and value to the customer. Gins will become increasingly sophisticated with the use of new technology to reduce labor and operating costs, while optimizing market value. Gin owners, managers, investors, and researchers will need to make informed decisions on the adoption of future technology. Introduction The development of the saw-type cotton gin, late in the 18th century, resulted in a dramatic increase in cotton production in the United States and thus the ginning industry. In the 1800's and early 1900's, refinements in the gin stand and additional equipment for cleaning, conveying and packaging began to replace plantation gins with centralized ginning installations. Since about 1902, the cotton ginning industry has been consolidating - small gins are going out of business or increasing capacity to become cost competitive. As harvesting practices changed from hand to machine, the need for additional seed cotton cleaning and drying equipment at the gins added to the ginning process. Notable trends in the cotton ginning industry include: the number and capacity of gins; bale size, density and packaging; seed cotton handling systems; cottonseed storage and usage; bale classing and warehousing; and environmental regulations and safety (Mayfield, 1992). The purpose of this paper is to provide some general U.S. cotton production and ginning statistics, along with identifying ginning industry trends with the goal of helping gin owners, managers, investors and researchers make informed decisions for future plans in the cotton industry. Information for this paper was gathered through telephone interviews of selected industry representatives. Trends in Cotton Ginning Operations Gin Size and Location Cotton production in the last 13 years has generally remained above 15 million running bales, with the highest production occurring in 2001, yielding 19.8 million bales (Figure 1). The number of gins has steadily decreased over that same time period and has declined at a rate of 50 gins per year since 1990 (Figure 2). In 2002, 921 gins operated in the U.S., as compared to 1,533 in 1990, a 40% reduction. The average annual volume of our U.S. gins has steadily increased and currently averages 20,000 bales per year. All indications are that these trends in gin numbers and volume will continue to move in the same direction. This trend will require the remaining gins to adopt new technology to increase capacity and deliver a timely and quality product. Most recently, cotton production regions began to shift to the Southeastern production region, resulting in dramatic changes in state gin numbers. The West has the highest reduction, with the Southwest and Mid-South not far behind (Table 1). The Southeast, with only 4% reduction in active gin numbers since 1994, reflects the most recent cotton growth area. Four states, Georgia, Florida, Virginia and Kansas had a net percentage increase during that time period. The United States Department of Agriculture National Agricultural Statistics Services (USDA-NASS) publishes a yearly report on gin locations, numbers and is categorized by size. Data from this report are shown in Figures 3 and 4. California has the largest average annual ginning volume per gin plant, followed by Virginia, Georgia, and North Carolina. Kansas gins are new construction and the average annual volume is high. New Mexico, Oklahoma and South Carolina have the lowest annual volume, which in part reflects their smaller production volumes and other special situations. Texas has the largest percentage of small gins under 10,000 bales per year (Figure 4). California has the highest percentage of large gins. The ginning trend across the cotton belt is for increased annual volume in the 20,000 to 40,000 bale categories, while gin numbers will decrease in the smaller bale categories. Smaller gins provide an important service, but it will be more difficult for them to afford newer technology and regulatory requirements. There will continue to be opportunities for the consolidating and modernization of gin plants where production trends allow for the increased ginning volumes. Seed Cotton Processing In 1972, the cotton module builder was introduced and was steadily adopted as a field storage and transportation unit. By 2000, about 98% of the cotton was handled in modules and about 75% of the new gins do not have suck pipes to unload trailers. Module trucks are used for field to gin yard transport and module feeders are utilized to feed the gin plant. As the number of gins decrease, these trucks will have longer transport distances. Many ginners have increasing problems with using module trucks on federal and state roads, and it is expected that those concerns will continue. Module feeders provide more uniform flow into the gin plant, increased seed cotton cleaning opportunities, and increased capacity. The trend is toward complete module handling systems from field to gin, with increased research and education on preserving the quality of seed cotton during storage. Transportation of all types (modules, cottonseed, bales, etc.) will be a major component of gin operational costs, as fewer gins attempt to serve an ever widening area. More efficient storage and transportation systems need to be developed to meet these growing demands. Increased knowledge of gin operations is placing more emphasis on drying and seed cotton cleaning systems. It is critical that more of the cleaning is accomplished before the gin stand, as less saw-type lint cleaning is used. Although gins must accept all kinds of cotton, including wet and trashy modules, equipment must be available to handle worst case conditions and the knowledge is needed to know when and how to use that equipment. New sensor technology (moisture, color and trash) has helped ginners to make informed decisions during the ginning process. This is accomplished by monitoring and reducing dryer temperatures whenever possible and increasing air flows, using heat or single stages of drying when needed, and conserving energy where possible. Gins are using fewer stick machines during processing and in some cases additional cylinder cleaners, both inclined and horizontal, are being utilized. Gin Stands Saw gin stand capacity has been static at 15 to 20 bales per hour and none of the ginning equipment manufactures expect to increase capacity in the near future. Typically, the capacity in the gin plant is limited by some other component such as cleaning and drying equipment or the bale press. Some new gin plants are just adding more stands to gain the added capacity. In older plants, ginners are looking at new technology to improve efficiency and capacity. One concern is the decrease in cottonseed size and problems with cottonseed going through the gin ribs and into the lint cleaners. Smaller cottonseed size will continue to be a challenge for ginners, including the added pressure of reduced gin revenue from cottonseed sales, as pounds per bale continues to shrink. Lint Cleaners Much emphasis has been placed on lint cleaners, both in research and new product development. There has been a trend to limit the stages of saw lint cleaners to improve turnout and reduce fiber damage, while increasing the usage of air-jet cleaners. Ginners are utilizing technology, such as gin process control, to by-pass equipment when additional cleaning is not needed. Recent developments include the Lummus Sentinel™ Lint Cleaner that eliminates the need for batt forming feed works that can cause fiber damage. The Continental LouverMax™ lint cleaner adjusts the number of grid bars to improve turnout. Current ARS research is focusing on improving cleaning efficiency, reducing lint loss, and reducing fiber damage. Moisture Moisture restoration has been one of the hottest topics in ginning circles. Moisture restoration prior to the bale press can increase press capacity, reduce hydraulic-press pressure, and bale-tie breakage. However, final bale moisture should not be greater than 7.5%, as recommended by the National Cotton Council's Quality Task Force. Excessive bale moisture can cause hydraulic-press pressures to increase, causing damage to the press and potentially degradation of the fiber during storage. Research has shown that the addition of moisture prior to the gin stand or reducing seed cotton drying can reduce fiber damage and improve capacity during ginning. It is estimated that 60 to 90% of the gins have some moisture restoration system at the lint slide, about 80% use moist air, and 20% have direct spray or combination systems. Less than 10 % of the gins use moisture restoration prior to the gin stand. Of those gins using moisture restoration systems, 25% use automated moisture measurements instruments, resistance measurement or non-contact systems such as radio frequency or microwave moisture measurement devices. The remaining use hand held meters. Nearly all meters are difficult to calibrate and keep calibrated and have problems with surface moisture. The trend is to make moisture measurements at different locations in the ginning operation for improved management. Additional research and education is needed to optimize this process and to determine limits necessary to prevent lint damage from excess moisture. Baling Systems For many gins, the bale press is the limiting factor in capacity and/or consumes the largest portion of the labor force. About 10 to 15% of the gins have fully automated bale tying and handling systems, which allows for increased press speed, reduction of labor and improved safety. Also, new bagging and bale ties are being utilized. Currently 83% of the ties are wire, 16 % plastic, and 4% steel bands. Plastic tie usage is popular with the textile mills and its usage will likely continue to grow. Bale coverings utilized by the industry are woven polypropylene 52%, both stripcoated and fully-coated bags, 39 % polyethylene film and 4% burlap. Many of the choices are driven by the end user, with probable increased usage of fully coated polypropylene bags. Gin Process Control Gin process control of one type or another is a technology that continues to grow. Identification of pre- and postfiber quality attributes helps ginners make informed decisions on equipment processing and operation. Uster® IntelliGin utilizes color, trash and moisture sensing to automatically control certain ginning operations (dryer temperatures, stick machines, lint cleaners and moisture restoration) throughout the ginning process. The Schaffner IsoTester® (GinWizard™) measures fiber properties from the bale sample to provide the ginner with timely data to modify gin processing. These technologies have been a catalyst in educating ginners on the effect of gin operation and moisture management on fiber quality. In the future, additional fiber quality measurements will be added to these systems to improve not only the management of the ginning process, but to improve the linkage between the producer and the textile mill. Additional Services The percentage of cottonseed directly fed to livestock has increased from 15% in 1980, to an estimated 60% in 2002. Gins, especially in new production regions, have increased cottonseed storage facilities to capitalize on this marketing opportunity. Certain value added processes, such as EasiFlo™ cottonseed, may help to open new markets and value for cottonseed. Over the past years many changes have been made in the classing and warehousing of cotton that have reduced cost and improved efficiency. In new production regions, gin warehousing has become a common practice while older regions utilize central receiving warehousing. As gins increase volume, more opportunities to provide gin direct marketing to customers will be available. Coupled with some of the gin process control technology, another trend is to warehouse bales by quality traits to increase warehouse capacity and reduce additional handling costs and bale packaging damage when fulfilling orders. Gins and warehouses are increasingly using electronic systems to more quickly and widely process and transmit information to improve handling and marketing of raw cotton. Permanent Bale Identification (PBI) keeps fiber and processing information constant throughout the life of the bale. The industry has quickly adopted electronic warehouse receipts (EWR), now used by about 90% of the industry. Many gins are doing away with the collection and storage of the traditional rack sample. This fiber sample has traditionally been used by mills or re-classed in case of disputes, but does not justify the need for additional storage and handling costs. The USDA Agricultural Marketing Service, Cotton Division continues to increase turn around time for bale classing. Average time from sample receipt to classification is less than 48 hours and in some cases, the same day. About 53% of the gins use internet based data retrieval for classing data. This fast data availability helps ginners to identify problems with equipment, either in harvesting or ginning. Although it is not current enough to manage gin operation, it can help provide information valuable to the ginner and/or producer on a timely basis. With the advent of new technology, training gin management and workers is an important component to improving gin operation efficiency. Each year ginning schools are offered by the National Cotton Ginners Association and USDA, located at one of the three ARS Cotton Ginning Laboratories in Stoneville, Lubbock and Las Cruces. The schools provide training from research and industry experts on basic ginning fundamentals, equipment maintenance, labor management and safety. Special topics are offered to keep even the most experienced ginner updated on new ginning trends. Summary The decline in gin numbers in the U.S. is far from over because of the efficiencies and increased services of higher volume gins. Ginners are looking for every opportunity to improve the bottom line by increasing capacity, volume, and value to the customer. Cotton ginning will become increasingly sophisticated with the use of new technology to reduce labor and operating costs, while optimizing market value. Utilization of gin byproducts, such as motes, cottonseed, and trash will find increasing value. Good business management practices, as well as machinery operation procedures and adoption of new technology, will be critical. No gin should be expected to follow all of these trends; however good management and training are required to be successful. History from the USDA website.
United States Cotton Ginning Company - Delaware 1913
MSRP:
$189.95
Was:
Now:
$149.95
(You save
$40.00
)
- SKU:
- newitem59248464
- UPC:
- Gift wrapping:
- Options available in Checkout

Add to Cart
The item has been added
United States Gypsum Company Delaware 1979
MSRP:
$79.95
Was:
Now:
$59.95
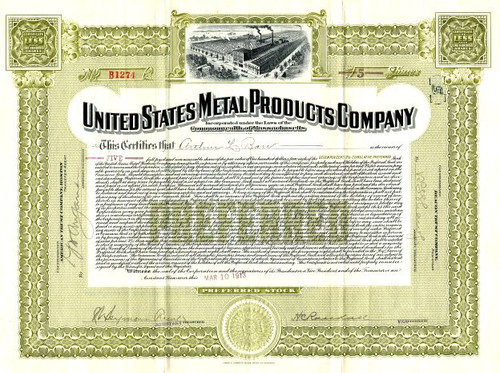
Add to Cart
The item has been added
United States Metal Products Company - Massachusetts 1913
MSRP:
$99.95
Was:
Now:
$79.95
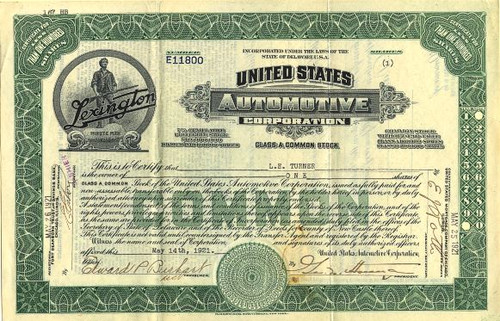
United States Automotive Corporation (Lexington Motor Company ) - Delaware 1921
MSRP:
$169.95
Was:
Now:
$149.95
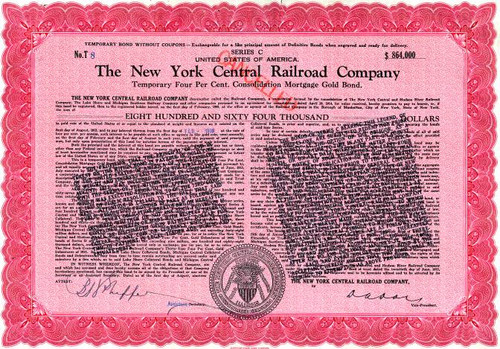
Add to Cart
The item has been added
New York Central Railroad Company $864,000 Bond - United States 1913
MSRP:
$189.95
Was:
Now:
$149.95
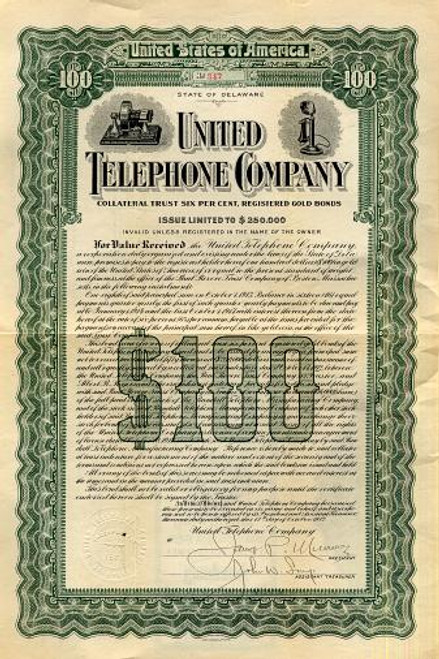
Add to Cart
The item has been added
United Telephone Company - Delaware 1912
MSRP:
$495.00
Was:
Now:
$395.00
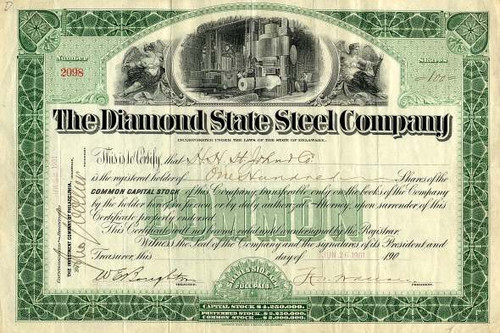
Add to Cart
The item has been added
Diamond State Steel Company - Delaware 1901
MSRP:
$129.95
Was:
Now:
$99.95
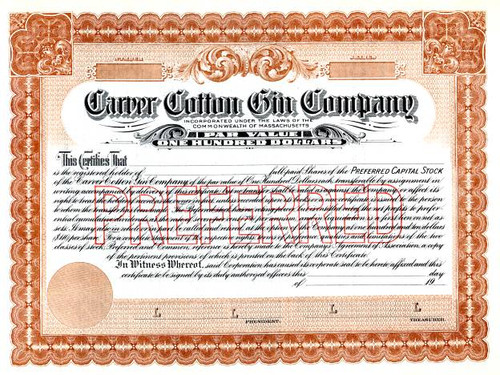
Add to Cart
The item has been added
Carver Cotton Gin Company - Massachusetts
MSRP:
$249.95
Was:
Now:
$199.95
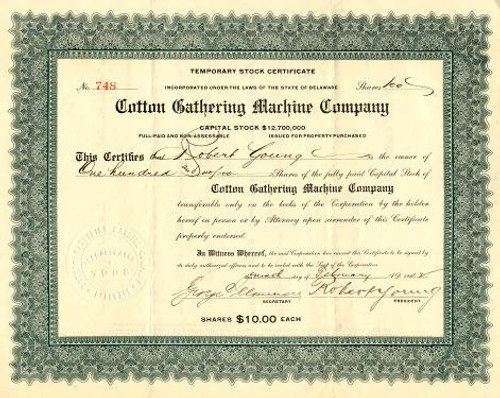
Add to Cart
The item has been added
Cotton Gathering Machine Company - Delaware 1912
MSRP:
$129.95
Was:
Now:
$99.95
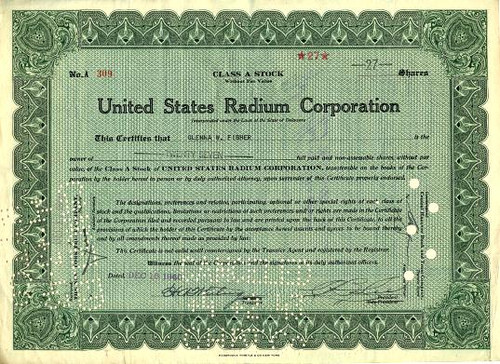
Add to Cart
The item has been added
United States Radium Corporation - Delaware 1940
MSRP:
$129.95
Was:
Now:
$99.95